Arizona Polymer Flooring Polyurethane 501 WB, 1.5 GL Kit
Product Highlights
- For professional use only
- Ideal top coat for areas that require maximum gloss retention
- UV-resistant
- Coverage: 200 to 350 sq ft per gallon
- Must order 1 Part A and 1 Part B for full kit
We pay the shipping charge, including hazardous material fees, on this item. There's no catch. No "buy this to get that" requirement.
Note: If your order contains items that are not eligible for free shipping, your order total will include our competitive shipping rates for those non-eligible items only. This shipping policy only applies to orders shipped within the Contiguous U.S.




Product Description
Polyurethane 501 is a high-solids two-component water-based aliphatic polyurethane. This unique material provides performance properties equal to conventional solvent-based catalyzed urethanes without the associated health and environmental problems.
Polyurethane 501 is VOC compliant in California. It offers substantial performance improvements over first generation catalyzed water-based polyurethanes, including higher film build capabilities, improved chemical resistance, and resistance to hot tire staining.
Polyurethane 501 provides hard, durable coatings that feature good gloss, easy cleanability, and superior abrasion resistance. Resistance to yellowing from UV light is excellent. For exterior desert applications, a special UV absorber package can be incorporated to ensure long-term chalk resistance and gloss retention.
Polyurethane 501 has been developed as a high-performance finish coat for various seamless flooring, coating, and architectural concrete applications where odor cannot be tolerated. It is the ideal top coat for areas that require maximum gloss retention, ease of cleaning, and resistance to heavy foot traffic.
Typical areas of application would include clean rooms, hospitals, concrete countertops, and high traffic retail areas. Polyurethane 501 is also suitable for aircraft hangars, automotive repair facilities, and garage floors. It is available in a satin or gloss finish.
Full kit requires 1 Part A and 1 Part B.
Return Policy:
Usage
Moisture Vapor Emissions Precautions
All interior concrete floors not poured over an effective moisture vapor retarder are subject to possible moisture vapor transmission that may lead to blistering and failure of the coating system. It is the coating applicator’s responsibility to conduct calcium chloride and relative humidity probe testing to determine if excessive levels of vapor emissions are present before applying any coatings.
Surface Preparation
Surface must be clean, structurally sound and free of chalk, wax, loose paint or curing compounds. Application over concrete requires the use of a primer. Previously coated surfaces must be mechanically cleaned and abraded with 100 grit sandpaper or sanding screen to ensure intercoat adhesion.
Mixing Instructions
Mix only that amount of material that can be used in a 3 hour period at 77°F. Higher temperatures reduce work time. In hot weather, it is advisable to mix smaller batches. Premix Part A before adding part B. Mixing ratio is 2 parts A to 1 part B. Add part B slowly while mechanically agitating part A with a slow speed drill. Mix for 2 full minutes until completely homogenized. Material cannot be properly mixed by hand. Use a small “squirrel cage” mixer for mixing small amounts.
Thinning
Material is normally applied as received but may be thinned with water up to 10% during application to keep a low viscosity. Any reduction water must be added after part A and B have been drill mixed.
Application Recommendations
Polyurethane 501 should be applied 200–350 sq ft per gallon by brush, roller or airless sprayer. Do not allow to puddle or accumulate in joint areas. Applications heavier than 200 sq ft per gallon will create bubbles in the cured coating. If multiple coats are required, and the material has cured for more than 24 hours, degloss with a black janitorial pad or fine sanding screen.
Handling Precautions
Use only with adequate ventilation. An appropriate cartridge-type respirator must be used during application in confined areas. Avoid contact with skin; wear protective gloves. Read Material Safety Data Sheet before using.
Slip and Fall Precautions
OSHA and the American Disabilities Act (ADA) have now set enforceable standards for slip-resistance on pedestrian surfaces. The current coefficient of friction required by ADA is 0.6 on level surfaces and 0.8 on ramps. Arizona Polymer Flooring recommends the use of angular slip-resistant aggregate in all coatings or flooring systems that may be exposed to wet, oily or greasy conditions. It is the contractor and end users’ responsibility to provide a flooring system that meets current safety standards.
Technical Specifications
State Restriction | Delivery is restricted to state(s) Alaska, Hawaii. |
---|---|
Color | Clear |
Category | Epoxy and Polymer Flooring Resin |
Gloss | High |
Brand | Arizona Polymers |
Type | Epoxy |
Condition | new |
Manufacturer Model Number | POLYURETHANE 501 |
solids (%) | 52 |

Documents
Special orders and drop-ship products that ship directly from the manufacturer do not qualify for our satisfaction guarantee and are not eligible for return, regardless of condition. Defects or damages must be reported within 48 hours of receipt in order to receive a replacement. Once placed, these orders cannot be canceled.Return policy
Real-World Knowledge Resource Center
-
Sign up for classes and training opportunities online or at a branch near you
-
Check out free how-to articles and technical tips prepared by our experts
-
Read our blog for the latest industry updates
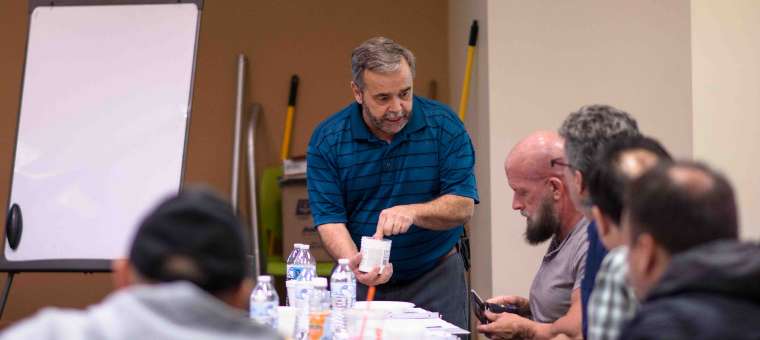
